Visibility: Clear
Current: Strong
Report: We have made some serious progress over the last two weeks! Last week, we received the remainder of our first round of injection molded sample parts and we picked up the first sample circuit boards from the assembler. It’s been a scramble to test everything. We need to make sure it all checks out so we can get back to our vendors as quickly as possible, and we know how anxious our backers are for their NEMO’s. We can’t wait to deliver, so we’re working extra hard to begin production.
Injection Molding:
Injection molded sample parts continue to be a success overall, despite minor adjustments that we have requested from the molders. For example, the O-ring grooves on the snorkel tube came in slightly too shallow, making it difficult to insert the snorkel tube into the NEMO intake. Fortunately, this is a relatively simple adjustment and it’s not a catastrophic failure.
Another change that has to be made is with the bearing races. These parts are made of a highly wear-resistant material that is different from the rest of the hard parts. They are inserted into the pump body, where bearing balls move back and forth as the pump pushes air from one side to the other. It turns out that this specific material did not shrink as much as originally expected, so the molders are in the midst of adjusting the shrink factor and reworking the mold so that the dimensions line up with the pump body.
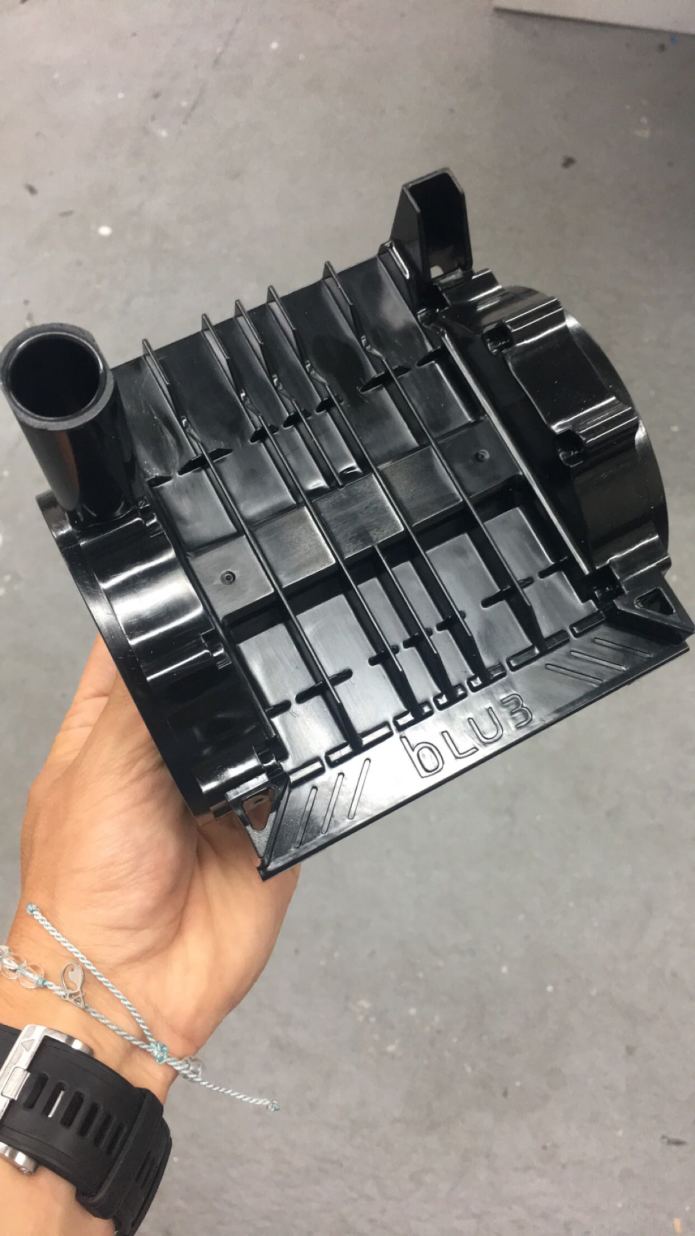
Injection Molded Pump Body – a very complex part!
Circuit Boards:
Last week we picked up the first circuit board samples from the assembler, located nearby in Fort Lauderdale, Florida. After performing functional tests to make sure that all subsystems are working properly, we used it to build into a full NEMO prototype.
With the circuit boards now finalized, we’ve been building our testing and calibration system for the boards. An electronics project box houses circuitry that will connect to the NEMO circuit board to test each subsystem automatically in only a matter of seconds. Next, it calibrates sensors and uploads the final firmware before the board is waterproofed.
Building the First Injection Molded NEMO:
On Friday we assembled the first NEMO using injection molded parts. We also integrated the production circuit boards. What an amazing feeling to fire it up for the first time! In previous prototype builds, it’s felt like minor steps forward toward a bigger goal. This build felt like everything coming together, like a solid plan finally coming to fruition. Although there are still adjustments to be made, we’re very confident in the overall design and path forward.
We’ve taken this opportunity to test out the assembly fixtures and tools that we’ve been working on over the last couple of months. Building a NEMO is now a breeze compared to our old prototyping methods. We’re about ready for production.
We will be test diving this unit so that we can analyze the performance and try to bring any major issues to the surface. Hopefully our dives will go as well as we expect! We’ll be sure to fill you all in on the next update.

The First Injection Molded NEMO
Forecast: Although we wish we could have delivered NEMO’s to you all by now, we are very satisfied with the progress we are making week to week. The final parts are still coming in, including foam flotation units and battery packs. We’re still making adjustments to the injection molded parts, and we have a little more work to do on the production line. We are right around the corner from building the first production NEMO. We thank each and every one of you for your support – we are almost there!
BLU3 Team