Visibility: Clear
Current: Moderate
Report: We are happy to share that NEMO’s first injection molded dive went extremely well. While some changes to molded parts need to be completed before finalizing the molds for production, the overall design is in great condition. Performance is better than ever, the parts look beautiful, and NEMO feels more like a final product than it ever has before.
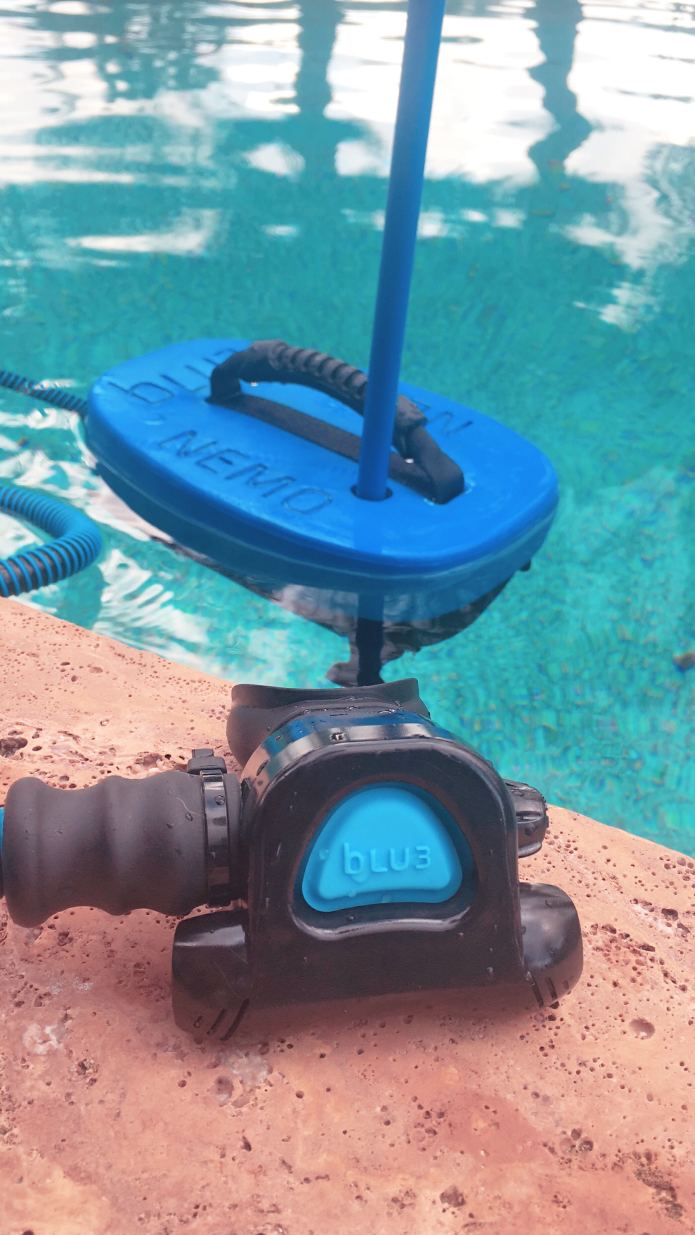
CE Compliance:
First off, some good news! We’ve successfully checked off all the boxes for self-certification of CE compliance. The CE marking is a certification mark that indicates conformity with health, safety, and environmental protection standards for products sold within the European Economic Area. We have been working with a CE consultant over the past 7 months to make sure that we are compliant with all directives and standards that apply to NEMO. The EMC testing that we wrote about in our Week 26 update was a major part of this.
As of yesterday, we have signed our Declaration of Conformity and we are ready to ship with CE. To maintain our compliance with CE we must monitor regulatory updates to the regulations and standards, and if necessary, make changes to the product or the documentation.
Foam Flotation Units:
We came across our first major part defect last week when we received our initial delivery of foam flotation units. Through the prototyping process of this part, the manufacturer built it out of two pieces glued together. We found that this method worked fine for prototyping, but the units were not durable enough to be used in the final product. For this reason, we specified with the manufacturer that the production units must all be built from one foam block and not two pieces glued together.
As it turns out, the manufacturer realized that they did not have the correct thickness of foam sheets and it would be an extra step in their process to source the sheets, so they decided to build the first production run with two pieces glued together anyway. When we opened one of the boxes upon delivery after 45 days of shipping by sea, we were devastated to find that the manufacturer had ignored our specification. It is especially frustrating to find such a simple mistake amidst so many other complex designs that are moving along smoothly.
Fortunately, we had specified in writing that the parts must be built out of one block of foam, and the manufacturer is making right by building a new production run and shipping us enough units by air at no cost to BLU3. They will keep more parts on standby in case we need additional foam flotation units on short notice.
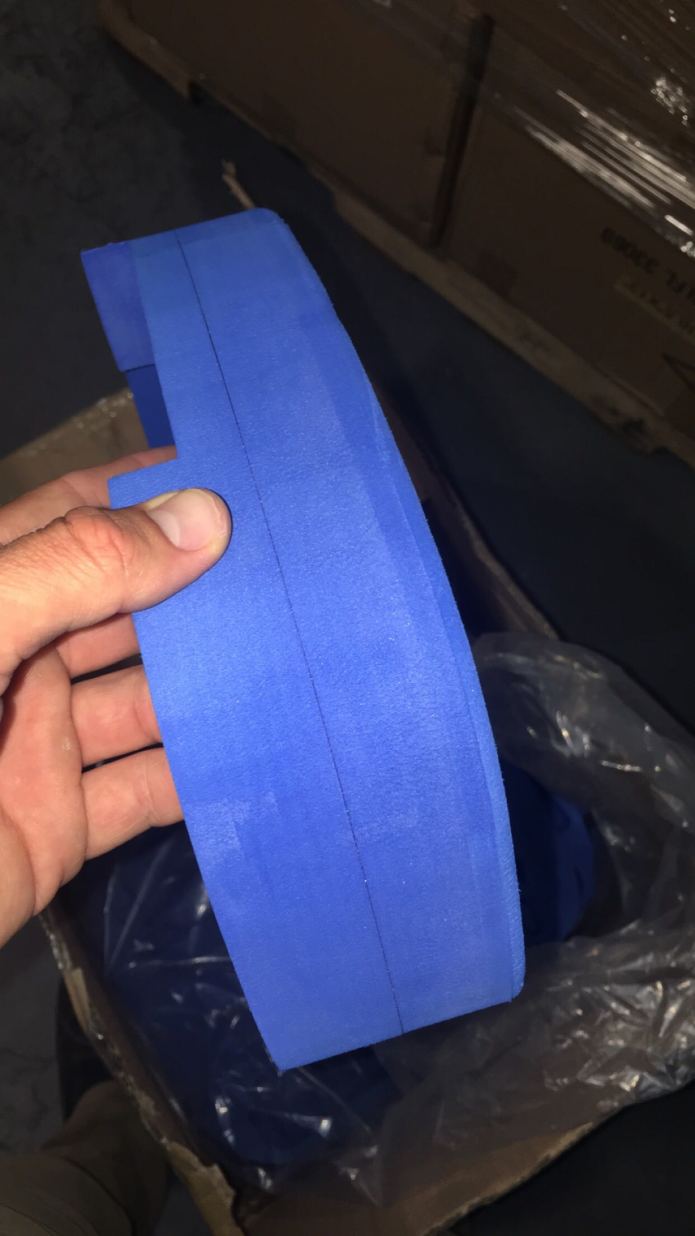
Battery Packs:
Battery pack production is underway. This is one component that has seen some delays and taken longer than originally anticipated. The packs are being built now and then they’ll be waterproof tested before they’re ready to ship. While it would be most cost-effective to ship the packs by sea, we are prepared to air freight enough packs to get started into production.
Our plan is to begin a partial sea shipment as soon as possible and have the battery manufacturer keep the remainder of the packs on standby to ship via air freight once we are ready for them. Since the battery packs aren’t quite required for the actual assembly process of a NEMO, we can wait until the other pieces to the puzzle are well lined up – primarily the injection molded parts.
Injection Molding:
Seven parts out of the first molded parts samples require some sort of change to be made. Some of the revisions are quite simple, while other changes have taken a bit of time to specify. For example, we found that both the regulator diaphragm and the end caps were made with too hard of a material. This is a relatively easy change because the manufacturer simply swaps out the durometer of the material they are using until we find the correct hardness. At least the overall dimensions of the design of these parts are correct.
In a few other parts we have found dimensional issues that affect the functionality of the design – namely O-ring grooves and bearing races. We’re dealing with parts that require precision down to the thousandths of an inch to function properly, so it can be tricky to get it right on the first try. We are confident that we’ll be in good shape with the next revision of parts but unfortunately, we don’t have an exact timeline yet on when to expect those parts. Once we can confirm the parts, the molders will add textures to all of the molds and then we’ll be ready to go into production.
Life Cycle Testing:
Remember the Breathing Machine? The automated diving simulation machine that we built so that we could run life cycle tests to figure out what parts inside of NEMO fail first, and if they last long enough to be deemed acceptable from a design perspective? Well we’ve got it back up and running, and we’re using it to test the first injection molded NEMO. So far NEMO has completed nearly 75 simulated dives without any issues. This is a great sign!
Forecast: The major hurdle now seems to be finalizing the revisions to the injection molded parts. In the meantime, we are still waiting for the delivery of some of the key components – circuit boards, foam flotation units, battery packs, dive flags, and a few other minor parts. We’re also still working out kinks on the assembly line and hiring our first assembly technicians. It is not unlikely that we’ll be ready to ship out the first production NEMO by the end of June, but we cannot rule out the chance of any other major setbacks. Thank you for your continued support.
-BLU3 Team