Visibility: Good
Current: Strong
Report: We’ve been testing our production prototype extensively and so far so good. This is really promising news! Our engineering team has been logging 12-13 hour days this week, let’s give it up to them for their commitment ?
We’ve received many parts and components for our production line and things are really coming together – we’ll share a photo of our progress in the next update. For now, here’s a look at us testing the production prototype:
Compliance Testing:
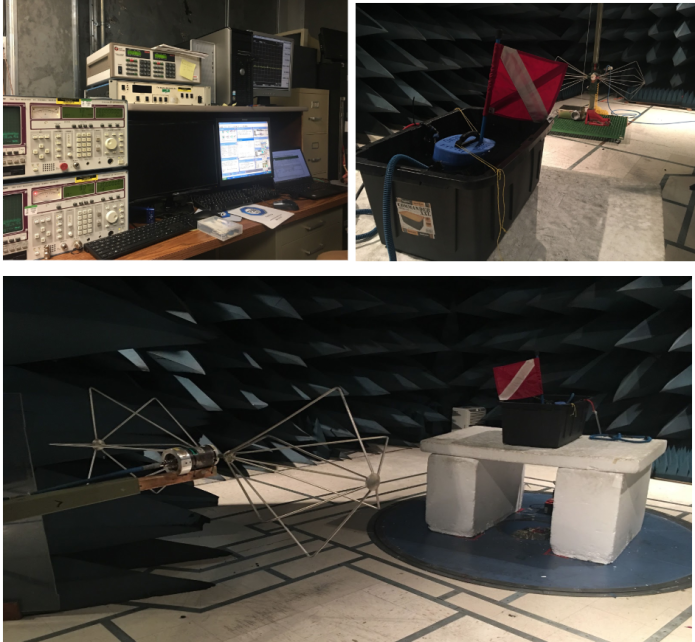
Two Nemo prototypes were taken to a compliance testing lab this week where the radiated electromagnetic emissions were evaluated. This test was a form of preliminary testing to get an idea of where we stand before proceeding into the full formal testing, which will take place over the course of 4-5 days in the beginning of April. The testing is a requirement for obtaining FCC and CE certifications.
Tube design upgrade:
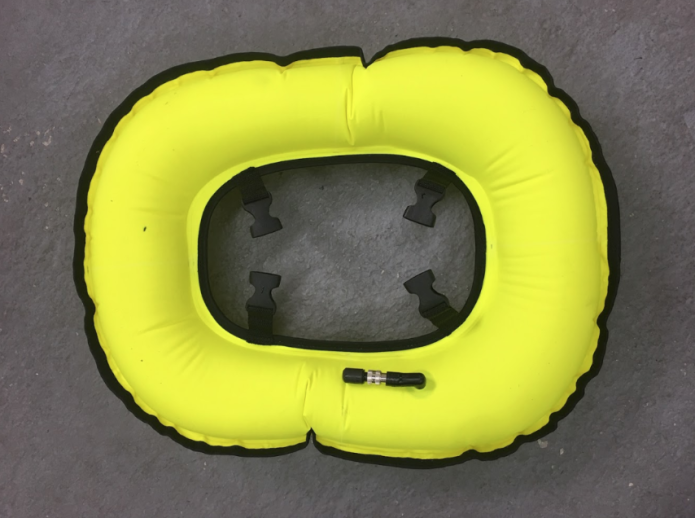
We recently revised the tube design and had our manufacturing partner make a new prototype. It’s now easier to attach the tube to Nemo and it’s a much more secure fit than before. Also, it now has binding on the inside circumference to protect the material and it boasts a buoyancy of 22 lb, which cleverly meets the buoyancy requirement for a Type 1 PFD life jacket! Production of the tubes is beginning as we speak.
Dive flags:
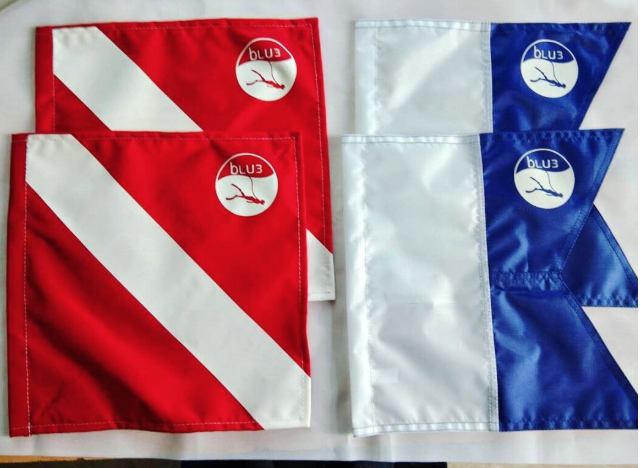
Our dive flag partners have really come through! Since we have orders from around the world, we made sure to have both the diver down flag and alpha flag options – you will be able to choose which flag you prefer when we send out the order survey in May.
Foam Flotation Units:
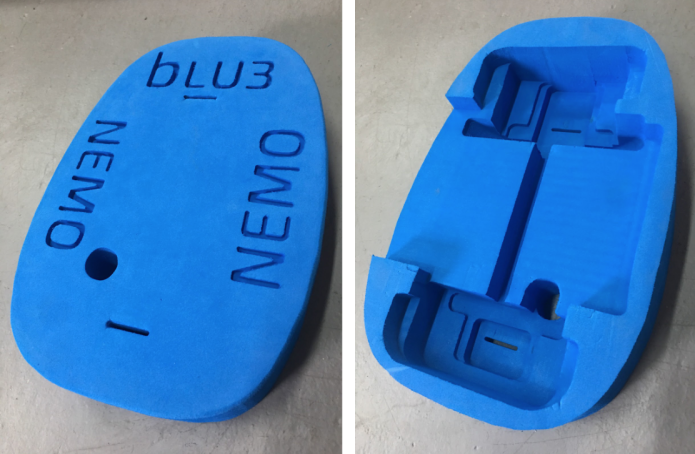
The first 500 flotation units have been CNC-cut and are about to be shipped out to headquarters. We’re very glad we found our supplier so that we don’t have to set up production CNC cutting in-house. We have begun building out production line tools for other assembly processes and hope to share more on that in the next update.
Forecast: We
are undoubtedly on a tight timeline with the injection molding, but if
everything moves along smoothly then we should still be on track to
build the first units in May. We’re anxiously awaiting the first sample
parts! Over the next month we will be ordering many more materials, such
as regulator mouthpieces, hoses, screws, and so on – basically all of
the short lead time items that we haven’t already ordered. While we’re
waiting on injection molded parts, we’ll be setting up the production
line so that we can produce units efficiently when the time comes.
– BLU3 Team