Visibility: Excellent
Current: Moderate
Report: We passed all of our Electromagnetic Compatibility testing, so we’re now finalizing the circuit boards and placing an order. Meanwhile, we continue to make advancements in setting up the production line, and we’re working on designing the custom packaging with the help of experts in the field! Exciting times.
Successful EMC Testing:
The team is proud to announce that NEMO has passed all necessary Electromagnetic Compatibility (EMC) tests. The purpose of these tests are to confirm and prove that a device can operate in its intended environment without affecting other devices and without being susceptible to other devices’ electromagnetic field waves. For example, you wouldn’t want your TV remote to block your cell phone from receiving phone calls.
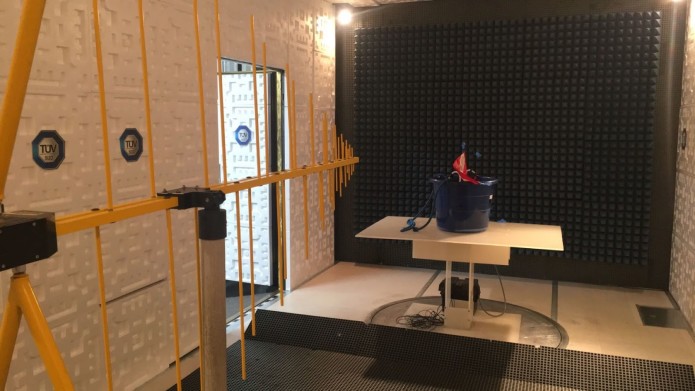
Successful completion of EMC testing is a requirement for communications certifications around the world, such as FCC in the United States and C-tick in Australia. Most certifications require only the emissions testing portion of the EMC test. Since we plan to deliver units into Europe, NEMO was also tested in the immunity portion, which is a requirement for CE certification and delivering units into Europe. There are still standards to check off the list before NEMO can be CE certified, but this testing was the major hurdle that the team has been staring down for some time now. We’re glad that’s over with! Here’s a few photos from the testing:
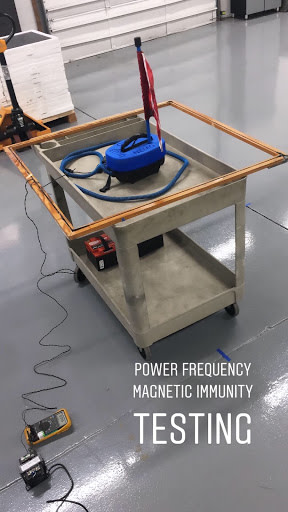
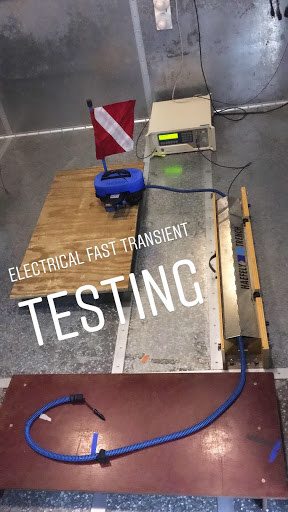
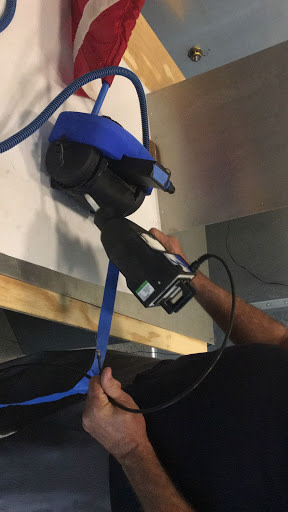
Finalization of the Printed Circuit Boards:
Given that the EMC testing is now behind us, the electronics boards are ready to be finalized and moved into manufacturing. Had the testing failed, the boards could have required modifications to limit emissions or susceptibility of electromagnetic fields, depending on which tests failed. Fortunately we passed with flying colors, so the team is currently in talks with several circuit board assembly vendors and will be making a commitment within the next week.
The vendors will take about 5-6 weeks to deliver production units. In the meantime, BLU3 engineers will be setting up the testing, calibration and programming fixtures for the circuit boards. These processes verify that all board components are working properly and they adjust the micro-controller’s baseline values to compensate for small variabilities from board-to-board. Each process will be mostly automated to ensure efficiency and repeatability of the production line.
Producing the Production Line:
With the injection mold tooling process underway, the engineering team has made the production line a top priority. Each assembly process has been fully defined and evaluated so the team is just moving down the line and crossing off process by process, in order of longest to shortest to complete. Critical-to-quality (CTQ) checklists for each process have been developed and the and the full Failure Mode & Effects Analysis (FMEA) is in progress.
With each assembly process, there’s a testing procedure to ensure the assembly was done correctly. For example, once the permanent magnets for the motor are placed into the connecting rod, it must be confirmed that the magnetic poles are facing the desired direction. The team recently built a tool that does exactly this – a 3D-printed fixture filled with electronics is placed on top of the connecting rod and the tool lights up LED’s to notify the operator whether or not the magnets are oriented correctly. Since an incorrectly oriented magnet would result in a significant amount of rework down the line, this testing process is worth the short amount of time it takes.
Custom Packaging:
With first deliveries approaching ideally in the next couple of months, we’ve started working with a few custom packaging suppliers. We’re about to send them all of the components of the product so that they can design us exactly what we desire in a package – it should facilitate low shipping costs, meet all requirements, use environmentally friendly materials, physically protect the product, and be aesthetically appealing inside and out. This is why we’re hiring the specialists!
Forecast: We have been pushing really hard for first deliveries to be completed in May. Depending on how smoothly a few major things go, this may not be possible. There tends to be unexpected delays here and there – that’s something we’ve come to learn that we can always count on. For example, our foam flotation units were randomly selected for inspection and held up in Chinese customs for a couple weeks, pushing back their already-tight delivery schedule. We do assure you that the team is working as hard as possible to bring NEMO to market as soon as possible. The light is at the end of the tunnel and so the motivation is higher than ever. A big thank you to all of our supporters who have made this journey possible!
– BLU3 Team